X-Axis Powerfeed for Mini Mills Part 2
The next step was to figure out how to package it so that it would
drive the mill. The first step was to create a coupler to connect the
shaft of the drill to the table leadscrew. The drill shaft was a standard
thread but I can't remember it for sure now. I believe it was 3/8 x
16tpi but don't quote me on that. At any rate, I created the following
coupling on my lathe:
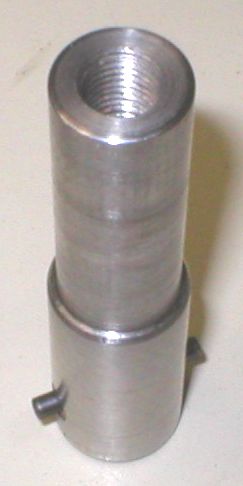 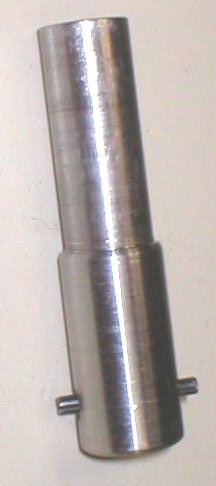
One end is threaded to fit the drill shaft. To allow it to
run in either direction without unscrewing itself I bored the other end and
drilled a hole through it to allow for the left-handed screw that held the chuck
on the drill. Note: I found out the hard way that you
need Locktite on the screw! The outside diameter of this end
is 5/8" to fit a bushing I happen to have quite a supply of in my junk
bin.
The other end is bored to fit the end of the leadscrew on the
mill. Fortunately mine included a leadscrew that already had a notch in
the end of it to connect a powerfeed so I put a roll-pin through the coupling to
fit into the slot. Before final assembly I cut the pin to the diameter of
the coupling.
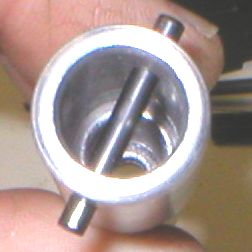
The next step was to figure out how to mount the motor. I
really didn't want to have to fight with turning the motor and gearbox whenever
I wanted to move the table manually so I had to figure out an easy way to mount
it that would allow me to disengage it. I decided that mounting it so that
the motor could slide in and out would be easiest so I let the coupling
described above slide through a 5/8" bushing and I used a block of plastic to
machine a similar arrangement for the motor to slide through as shown below:
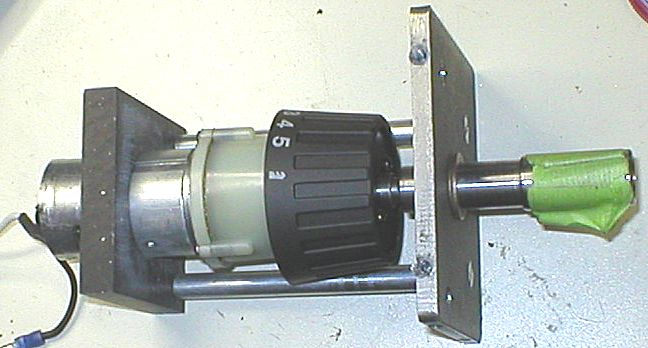
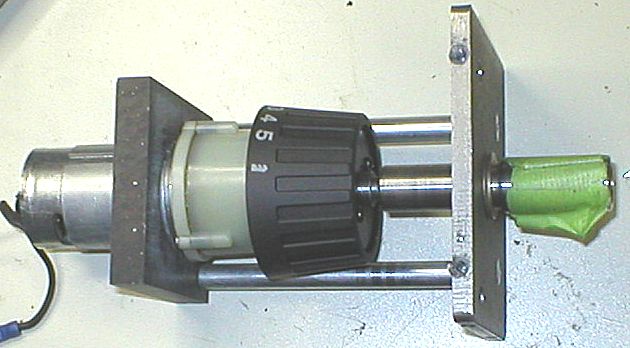
The block I used for the mount is a sample of a resin kitchen
countertop, similar to Corian. I picked up a box full of them at a thrift
store a couple of years ago just for this type of thing. The sheetmetal
wrapped around the motor that looks like a shim was not added by me. It
came that way. The green tape is just there to hold the left-handed screw
to the coupling so I wouldn't lose it.
Now I needed a way to slide it and a way to hold it in the engaged
and disengaged positions. I figured a spring would be good to engage
it. That way I could just release it and the spring would force it to
engage as it turned and reached the point where the roll-pin would drop into the
notch in the leadscrew. I ended up putting a lever on the front of the
motor and connecting a spring from it to the front plate to pull the motor
toward it like this:
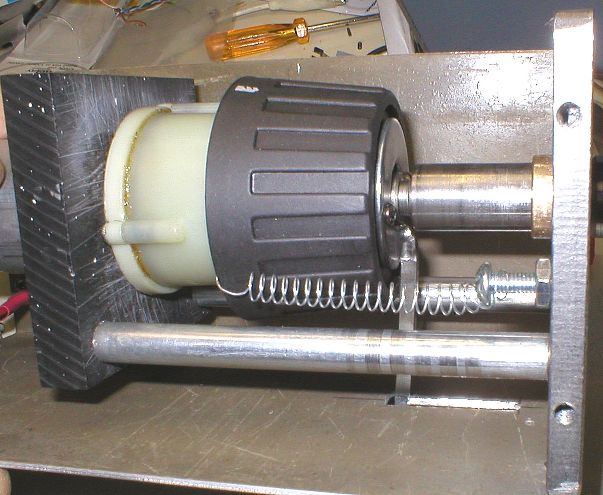
I cut a slot in the bottom of the case with a notch to hold it in
the disengaged position like this:
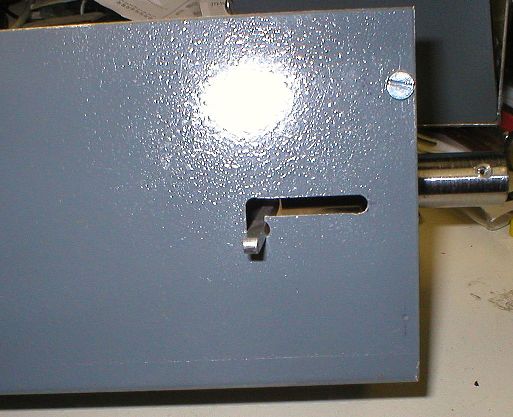
<Prev Next>
|