X-Axis Powerfeed for Mini Mills Part 3
The last step was to complete the case and mount the
controls. The ends of the case are 1/4" steel plate. I made the rest
of the case out of an old aluminum panel I had lying around. The picture
below shows everything mounted on the front panel except the heatsink for the
MOSFET. The black object toward the lower left corner is the switch
housing from the drill. The two blue objects to the right of it are the
relays that I used to switch the motor
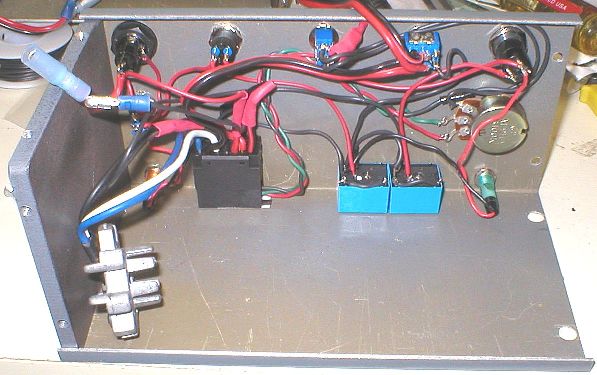
Here's an outside view of the front panel:
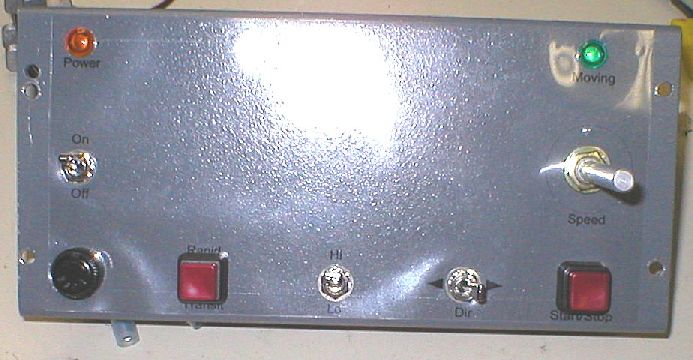
First an explanation for the lousy label job. I like to draw
labels with a CAD program and then reverse them and print them on a transparent
sheet usually used for overhead projectors. I then normally spray them
with spray-on contact cement but I was out of it this time and was in too big of
a hurry to get this thing going so I put it on and let the installed controls
hold it in place. You can tell from the above picture that this didn't
work so well and I also need to move a few of the labels around so someday I'll
redo it. For now though I'll leave well enough alone. It did have a
tendancy to allow chips to fall behind it so I added a strip of tape to the top
to seal it.
I added an amber light to show when power is switched on and
a green light to show when the motor is being driven.
The round black item in the lower left corner is a fuse holder.
So far I'm very happy with the end result. It works really
well and saves me a lot of cranking. After a bit of adjustment the clutch
slips if I forget to unlock the X-axis, and at end of travel but I don't believe
it's ever slipped for normal cutting.
Here's the finished product:
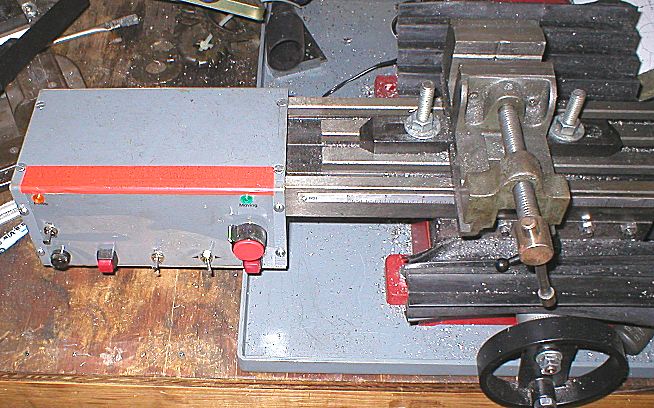
The only problem I've had is that I should have adjusted the
lead screw before I made the mounting plate because it's not exactly centered at
the powerfeed end and this causes it to tighten up near the end of travel in one
direction. The only other thing I would do different if I built another
one is to mount all of the controls toward the left end of the case because the
speed knob and start/stop switch are a bit hard to get to when the table moves
all the way to the right.
As for a parts list, I don't really have one but here's a basic
rundown of the electronic parts without specific part numbers. There are
many different styles available so you can pick whatever you like.:
-
Power switch, SPST
-
Hi/Lo drive switch, SPST
-
Left/Right switch, SPDT
-
Rapid Traverse switch, Momentary pushbutton
-
Start/Stop switch, Latching pushbutton
-
Lights are LEDs with dropping resistors for 12VDC
-
Speed potentiometer, 100KOhms
-
Relays, SPDT, 12VDC Coil, 10 Amp Contacts
Total cost for the whole project was around $30-$35 but I already
had all of the mechanical parts except for the drill itself, and a few of
the electronic parts. I paid a premium price for a couple of the switches
and the relays because I wanted them in a hurry and Radio Shack is a bit pricey
and the only game in town. IIRC a SPST switch like the one I used for the
power switch is about $3 but if you order from someone like Mouser, MECI or MPJA they're more like $0.45
so if you want to build one of these it would be cheaper to plan it out and
order all the parts you need before starting. Of course shipping will eat
at the savings quite a bit so it's usually best to order everything from one
dealer. Plus it never hurts to order a few spares at that price!
Obviously this isn't the best way to do it but it works surprisingly well and
was really cheap and easy to do. At first thought the drill seemed a bit
too simple but it really does offer a great solution. The motor and
gearbox can handle the torque and the clutch saves you the trouble of having to
sense end of travel either via a torque/load increase or switches to turn the
motor drive off.
I think that pretty well covers it but of course you can email me if you have
questions.
<Prev Back to Milling>
|